Apixa goes through great lengths to select the best imaging hardware for any specific application needs and constraints. Depending on the application, an estimation of the operating characteristics of the setup might still be needed, with varying accuracy demands. Typically we aim for a no-calibration design or direct utilization of the proper off-the-shelf calibration software and targets.
However, if the setup is atypical, we engineer the best solution possible. Our expertise extends to stereo and multi-camera systems, line-scan cameras, various lens types and distortions, structured light and camera systems, color and hyperspectral sensor calibration, various 3D sensors, camera and conveyor belt systems, self-calibration, auto-finetuning, and calibration targets for very small or large field of views and working distances.
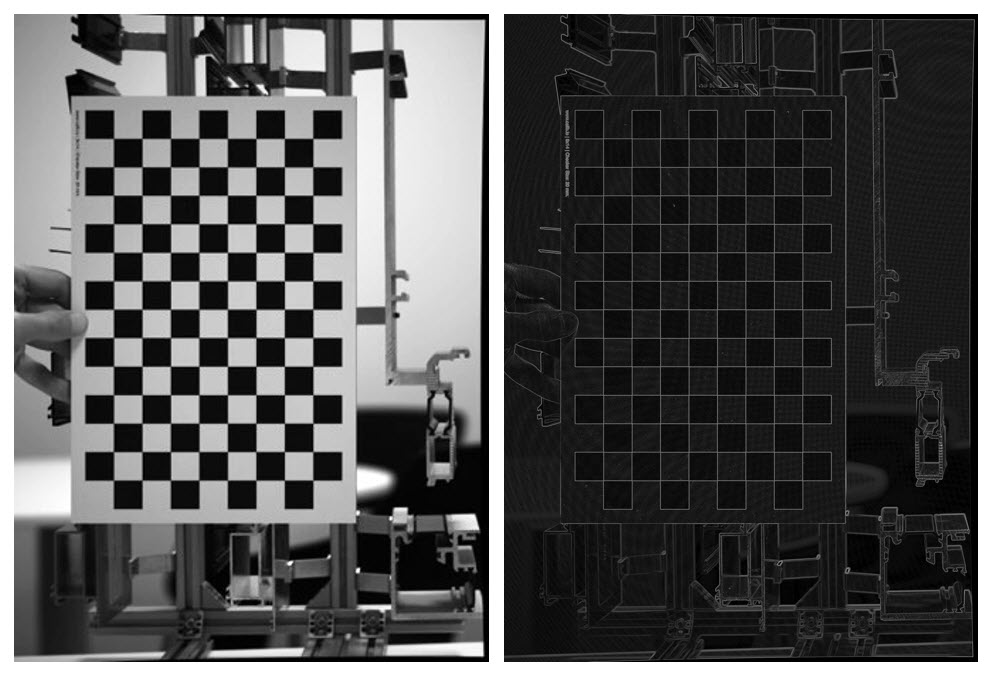
Multi-camera systems
Stereo and multi-camera systems are utilized for better coverage of the target 3D scene and sometimes to recover the lost depth information due to a 2D imaging process. To fuse such information from multiple imaging sources at different vantage points, it typically becomes necessary to know the camera's internal transformations and external positioning with respect to each other and target scene elements, such as the ground plane for example.
The procedure complexity and accuracy must accommodate the specific needs of the project, for example, unique identification of products on a 2D belt can require only moderately accurate 2D calibration whereas a 3D inspection task requires typically accurate 3D calibration. Further variations on the system will possibly render many off-the-shelf components less applicable, such as deploying special lenses, line-scan cameras, large or small scene sizes, limited depth of fields, occlusions, and independent sub-systems on a moving stage, etc. Thanks to our proven record in such setups, we can provide a custom solution if needed.
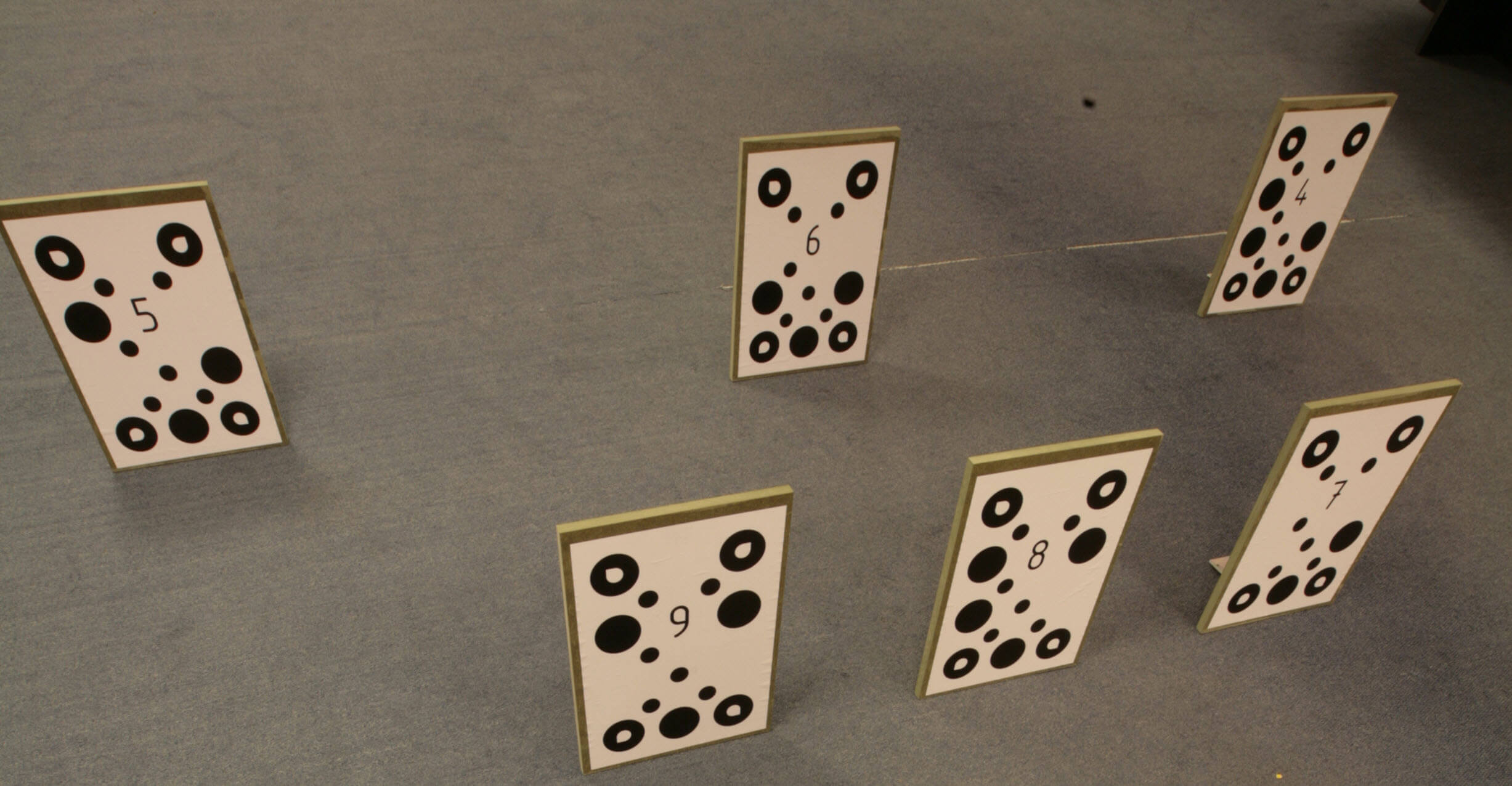
Structured light camera systems
Structured light is a popular approach to obtain 3D shape information in low-lit or textureless target scenes. Structured lights come in different varieties such as single laser stripe, multiple stripes, a regular or random grid of dots and more. Correct localization and identification/labeling of the individual components in the light source and formulating its relationship with the viewing sensor(s) are essential for accurate 3D measurements. To accompany the procedure, a proper calibration target typically needs to be selected/designed. We created calibration procedures for such systems for different target scene scales, from a few centimeters to tens of meters.
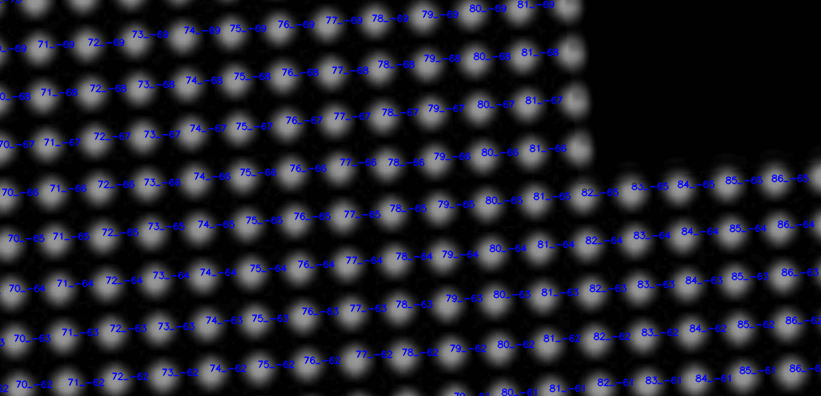
Calibration setup for hyperspectral cameras
Hyperspectral cameras offer the capability to inspect object composition, quality, and defects to a degree unattainable with standard RGB cameras. They can capture distinctive signatures of chemical composition by gathering intricate spectral information regarding object's light reflectance, transmission, and absorption across a broad spectrum of wavelengths. The output from hyperspectral cameras can be harnessed to train AI models and generate precise metrics for decision-making purposes.
Given the considerable cost associated with building AI models, it is important to avoid the need for retraining due to undesirable variations in the camera's outputs that are unrelated to the inspected objects. Several examples of factors that may cause unwanted variation in hyperspectral measurements include:
- Influence of environmental temperature on the spectral reading of a sensor without active cooling (e.g., outdoor temperature influence on a light-weight drone-mounted camera).
- Varied image integration times resulting in varied measurements due to the time-dependent impact of electron leakage in the sensor.
- Discrepancies in spectral responses among different hyperspectral cameras from different brands or even within cameras of the same brand, especially when replacing or upgrading equipment.
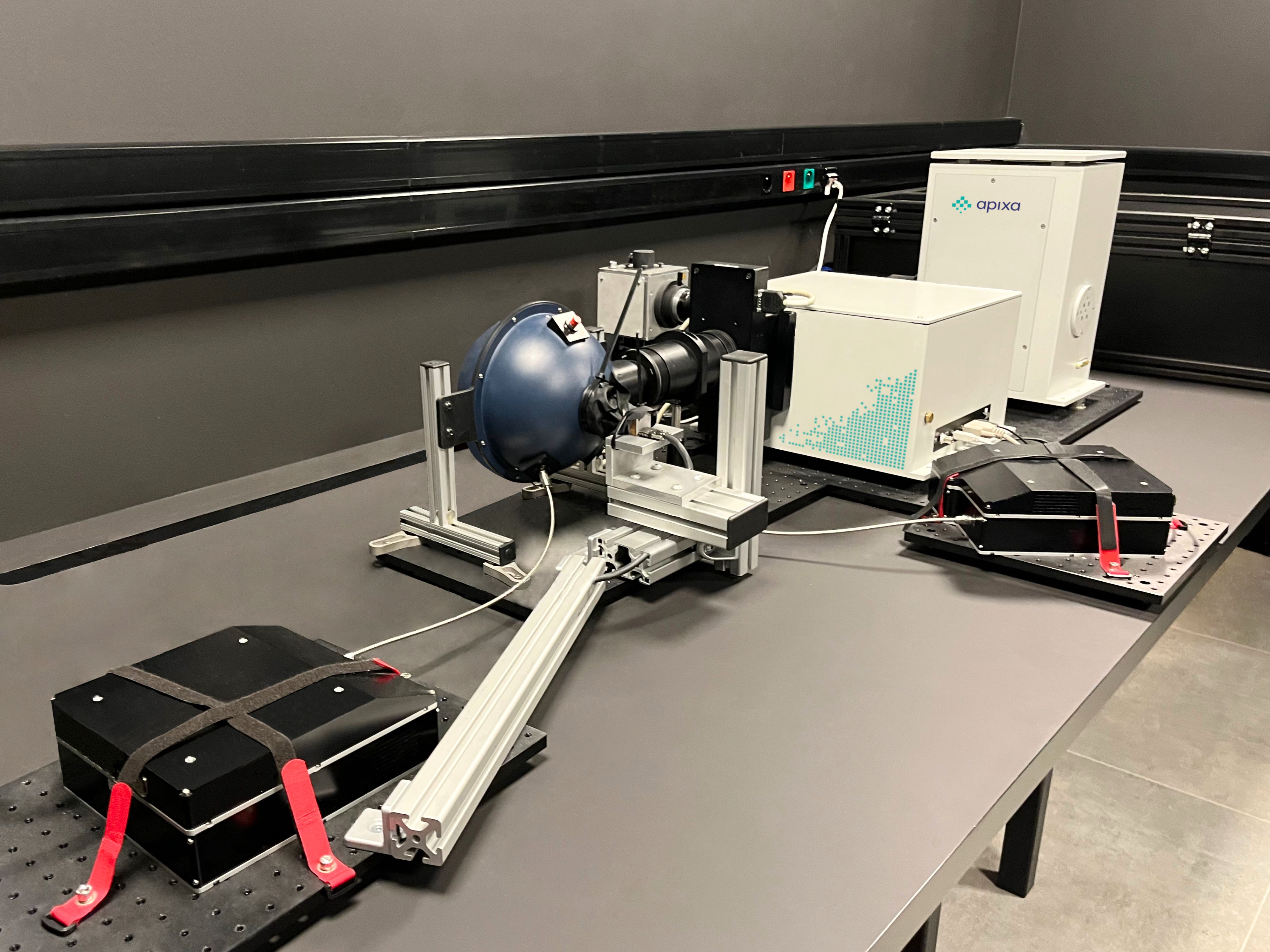
To accurately measure sensor responses and compensate for the unwanted effects, we have built a dedicated calibration setup for hyperspectral cameras. This setup incorporates a monochromator and various types of highly stable light sources to enable scanning through the entire UV to SWIR wavelength at high precision. Multiple high-end, actively-cooled, high-resolution spectrometers provide ground truth measurements of the light within a high-grade integrating sphere that is presented to the hyperspectral camera under calibration.
By recording the sensitivity of each pixel of the camera to individual light wavelengths, we can algorithmically compensate for temperature effects, integration time impacts, and other variables. Consequently, we can convert raw hyperspectral measurements into robust data, as if generated by an ideal hyperspectral camera.
Conveyor belt sensor systems
Correct co-calibration of imaging components and motion units in industrial settings is essential for different inspection applications that require accurate 2D or 3D analysis. Line-scan and area-scan cameras, laser depth profilers are typical sensors in such settings whereas active elements may also exist such as manipulator arms or printer heads. Thanks to our track record of calibrating such systems with different complexities and performance requirements, we can help you to choose the right approach for your application.
Self-calibration and photogrammetry
Especially in uncontrolled environments, vision systems can get de-calibrated. It is also possible that a factory calibration may not be even feasible in the first place. In such settings, it is desirable that vision systems can re/calibrate themselves by just using the environmental constraints, with little or no input from the user. On one end such operation can be mere finetuning of the parameters. On the other extreme, this can be the main engine behind the solution, such as in photogrammetry applications, where 3D scene structure and vision system's free ego-motion are estimated simultaneously.
Photometric calibration
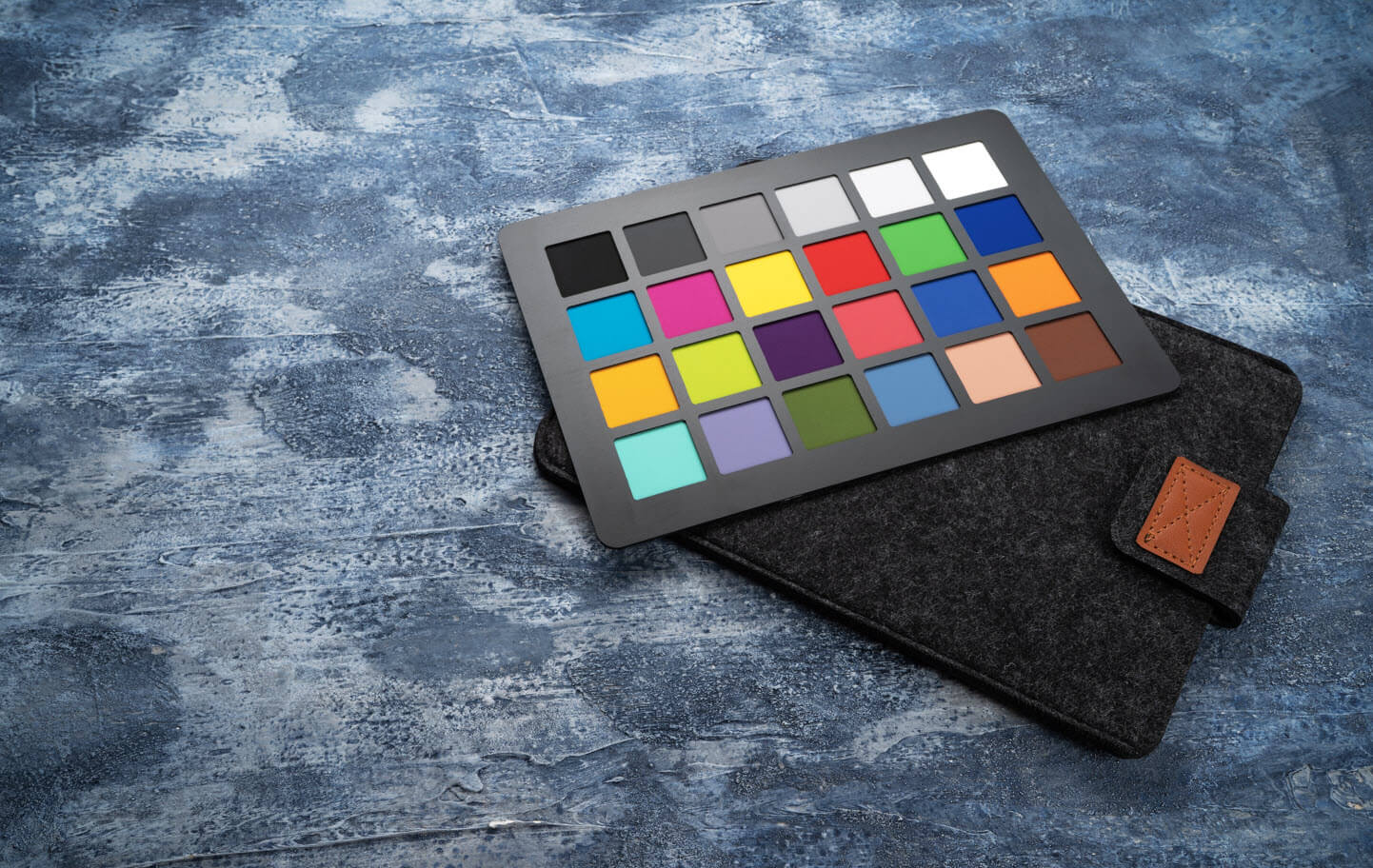
Many visual recognition tasks require the correct perception of color in the target scene. This not only ensures the consistency of the system performance, as more systems are installed but also simplifies the training dataset requirements and recalibration efforts. Hyperspectral sensor calibration can be considered as an extension of this concept. If the application permits, the use of pre-calibrated color targets can be good enough. In more demanding cases, we are happy to share our good understanding of the physics behind the image formation process to find the right solution.